Advanced Manufacturing Demands an Advanced Workforce
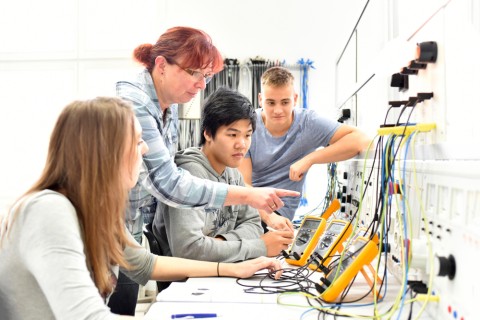
While recent headlines have focused on tariffs and trade policy, a quieter consensus has emerged across party lines: reshoring critical industries is now a national priority. The debate is no longer about whether to bring key sectors like advanced manufacturing back to the U.S. — it’s about how to do it.
Much of the current policy focus revolves around financing new facilities and incentivizing capital investment, which is a natural emphasis given the scale of infrastructure required. But the long-term success of these efforts will depend just as much on something less visible but equally vital: whether states are cultivating the skilled workforce needed to power these industries.
Advanced Manufacturing Comes into Focus
As policymakers look to bring critical industries back to American soil, advanced manufacturing has emerged as a centerpiece of this effort. Reshoring isn’t just about producing more — it’s about producing smarter. From semiconductors to electric vehicle components, the future of American manufacturing will increasingly depend on industries that blend cutting-edge technology with skilled labor. This makes advanced manufacturing not only a key driver of economic growth but also a strategic priority in the broader conversation about national competitiveness and supply chain security.
Advanced manufacturing refers to the use of innovative technologies to enhance products and processes: combining automation, high precision, mass production, and integrated information technologies throughout the production system. This sector includes industries such as aerospace, automotive, electronics, and renewable energy, where companies generate most or all of their revenue by converting raw materials and components into finished products through these advanced methods.
The significance of advanced manufacturing lies in its potential to drive economic growth, strengthen national security by reshoring critical supply chains, and create high-quality, future-ready jobs for workers across the country.
According to EnterpriseKC, a local think tank dedicated to regional development of advanced manufacturing in Kansas and Missouri, more than 114,000 Kansans and 280,000 Missourians have advanced manufacturing jobs now. The industry is expected to grow over 8% in both states over the next decade without accounting for future investment from all levels of the government.
Yet even as these industries expand, both states face a growing challenge: building a workforce capable of meeting not only the demands of advanced manufacturing but also filling talent gaps across the broader economy
Meeting the Workforce Challenge
Kansas and Missouri have taken important steps to support workforce development in advanced manufacturing, but much work remains. Both states have made marginal investments in career and technical education (CTE), apprenticeship programs, and industry partnerships to strengthen training pipelines. In Kansas, programs like Excel in CTE provide free college tuition for high school students in technical programs, while Missouri’s Fast Track Workforce Incentive Grant supports adults pursuing high-demand fields.
Still, ensuring long-term workforce readiness will require a broader strategy. That means aligning K-12 education systems to spark early student interest in STEM and manufacturing careers — integrating hands-on learning, robotics, and skills-based education long before graduation. It also means expanding dual credit and work-based learning opportunities, and providing postsecondary incentives for students to pursue advanced manufacturing credentials.
As states compete to attract major capital investment, the question isn’t just whether Kansas and Missouri can build the facilities — it’s whether we can build the workforce for the long term.
Aligned’s Take: Reshoring advanced manufacturing is an exciting opportunity for our region, but talent will determine success. Now is the time for state and local leaders to double down on education and workforce strategies that prepare students — from kindergarten to career — to thrive in these industries. If we want to be leaders in manufacturing again, we must start by making sure our students see themselves in the future of this work.